MIG Welding Stainless Steel Guide: Choosing the Right Techniques and Electrodes
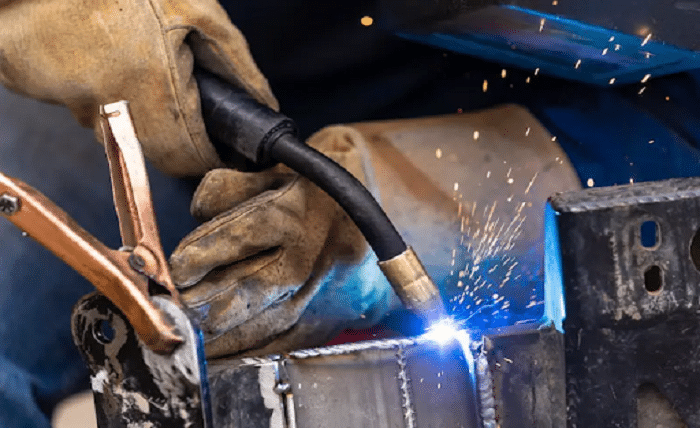
MIG stainless steel welding is a field that necessitates expertise, experience, and the right equipment. Stainless steel is ubiquitous in many industries due to its strength, corrosion resistance and good aesthetics — it so happens that proficiency in welding stainless steel has become increasingly critical.
Note: Discover the best stainless steel welding wire with us! As an authorized dealer of all major brands used by professionals, we offer the largest stock of welding supplies. Visit our website at https://www.udo.co.th/product/detail/yawata-316l-16 to explore our products or seek expert welding advice from our specialists. Don’t miss out on the highest quality and availability in the market!
Simply the knowledge of basics could create a difference between spending money on stainless steel electrodes, later getting wires with conclusive results or gaining proficient welding. Let us go through the process and how to make sure that you get the best results.
Step 1: The Fundamentals of MIG Welding Stainless Steel
Metal Inert Gas (MIG) welding (or Gas Metal Arc Welding, GMAW), is a major process for welding that works well with stainless steel. The method has been through feeding the moderate wire electrode within a welding gun which melts and merges to the basic materials below a shielded gas.
Why Use MIG Welding for stainless steel?
Speed: Compared to other processes like TIG welding, MIG welding is faster and works well for more extensive projects.
Precision: It gives you extreme control over the welding arc, which is important for preserving stainless steel properties.
Universality: It is suitable for various grades of stainless steel, including austenitic, ferritic and martensite
An answer lies in the welding methods and electrodes used to ensure a first-class weld.
MIG WELDING STAINLESS STEEL – KEY TECHNIQUES
Choosing the Right Gas for Shielding
The weld pool is protected from the surrounding environment by a covering of shielding gas. For stainless steel, a blend containing argon + CO₂ (usually 98% Ar and 2% CO₂) is generally suggested. This reduces the oxidation and thus keeps it from being oxidized between the weld.
Establishing well-defined parameters
You can also play with the voltage, amperage, and wire feed speed if necessary in order to maintain a stable arc while minimizing defects. Here are some guidelines:
Voltage — Gives a steady, smooth arc characteristics.
Output Amperage: Set a certain output amperage based on the thickness of the stainless steel
Wire Feed Speed : This should closely be determined according to the thickness as well as welding position, when not not properly adjusted could result in excessive spatter or poor penetration.
Using a Push Technique
If you are welding stainless steel using MIG, you can always use the push technique (pull away from the weld puddle) to get better visibility and less chance of contamination.
Preheating and Cooling
Preheat is not always necessary for stainless steel, however preheating to some degree can help to prevent distortion in thicker materials. After welding, providing uniform cooling to the material minimizes warpage and keeps the metal stable.
Selecting the Correct MIG Wire for Stainless Steel
The key to strong and even welds is the right electrode choice. Here’s what to consider:
Electrode Type
The type of electrode used must correspond to the type of stainless steel being welded. For example:
308L: Good for the welding of 304 stainless steel
316L: Great for welding 316 stainless steel, especially in high corrosion resistance applications.
You can have a closer-to-premium-performance product with Yawata 316L-16 that provides you durability of no-lower than 316L class electrodes.
Electrode Diameter
Effective choice for diameter according to material thickness:
To get better control and less heat input, use smaller diameters for thin material.
Bigger size for deeper penetration: Choose bigger sizes of thick stuff
Compatibility with Equipment
Make sure that the electrode is compatible and within the specification of your MIG welder to maintain efficiency and consistency.
MIG Welding Stainless Steel: Common Issues You Might Face
Even when you have the right tools and techniques, difficulties can occur. Below are a few common problems and the corresponding solutions:
Oxidation and discoloration: A clean shop along with quality shielding gas will go a long way in avoiding oxidation.
Warping: Avoid heat distortion by utilizing proper clamps and cooling techniques.
Cracking: Have sufficient joint preparation along with proper prevention of excessive heat input to avoid cracks in welds.
Beginner Tips for MIG Welding Stainless Steel
Test Run on Scrap Material : Practice welding on scrap stainless steel before tackling the final piece.
Ensure Contamination Free Work Area: Any sort of contamination is not suitable for the weld; Make sure that the base metal is clean prior to welding.
Buy Good Supplies: Purchasing quality electrodes such as those offered at UDO Welding can help improve your outcomes tremendously.
The Importance of Quality Electrodes
Your electrodes are crucial in determining the strength, toughness and visual appearance of your welds. Low quality goods cause spatter, erratic arcs or weak welds. There are great, reliable options such as the Yawata 316L-16 electrode where your precision and performance are guaranteed for professionals and hobbyists.
Conclusion
It is a high-value skill that needs detail-oriented techniques and top-shelf materials for MIG welding stainless steel. You can use the right shielding gas, optimize welding parameters and purchase high-grade electrodes like Yawata 316L-16 to produce amazing quality weld joints that last. So whether you have experience in welding or are simply a hobbyist, you now hold the key to an unending world of possibilities when it comes to stainless steel welding.
Uncover your ideal welding supplies today, and enhance the quality of your work at home with ease. Click here and please follow UDO Welding for more updates as well as premium products that suit your needs!